We are the leading effluent treatment plant manufacturer dealer and supplier in India, call us on 9040005060, 9861336272 as a leading ETP Effluent Treatment plant (ETP) manufacturer in India.
Effluent Treatment Plant Process
a) Pre-treatment
Effluent Treatment Plant process Odisha India includes a classic pre-treatment unit with a preliminary coarse screening followed by fine sieving for the whole of the throughput. The separation process continues with the effluent being directed to the dry weather biological channel up to a flow of 8.2 cubic meters/sec. The excess flow is directed to the wet weather channel to a maximum of 16.4 cubic meters/sec.
b) Biological treatment
The dry weather flow is sent to grit and oil removal before being processed in 12 biological treatment channels. Each of these channels has first a biological degrading zone for phosphorus, followed by one for carbon and nitrogen (AZENIT-P® process( cfr section 6)). The effluent is then sent to basins where the treated water is clarified through decantation of the biological mud. Part of the decanted sludge is sent back to the start of the treatment process to be fed into the biomass. The clarified water is sent out to be returned to the Senne. Waste Water Treatment Plant process in India is very quick now-a-days.
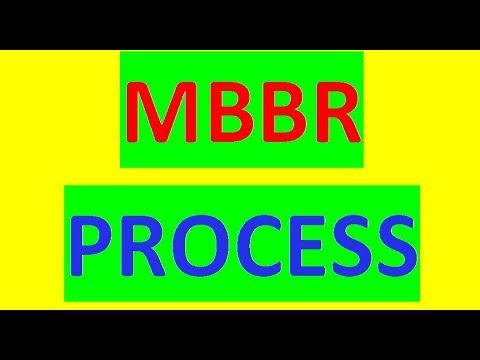
c) Wet weather treatment
Wet weather is characterized by a re-suspension of the solid material that had sedimented in the network through dry weather. The treatment of this sewage requires specific techniques.
The wet weather flow is first sent through a rough grit removal to eliminate particles bigger than 300 micrometers (MECTAN® process). Then it is settled using the ACTIFLO® process (cfr section 6). This rapid settling technique involves lumping the effluent together using a coagulant and then mixing it with sand. With its high density, the sand speeds up the separation out of the agglomerate in the decantation stage. Effluent Treatment Plant Process Odisha India
d) Sludge Treatment
a) Process
The principle is to break down the organic material in the sludge so as to obtain an entirely mineral final residue. This break-down process uses two complementary procedures: digestion in the anaerobic phase and wet oxidation.
- Preliminary conditioning
After exiting the water treatment stage, the sludge is first thickened in cylindrical structures in each of the process lines, both biological and wet weather.
The sludge is conditioned with a polymer to facilitate decanting before it is guided into the structures.
The sludge is then extracted and pumped into a common storage area in preparation for dehydration. This is done using centrifuges. Four treatment lines with one as back up are planned for this stage. After dewatering, the resulting residue is stored in a silo for the next stage.
- Digestion in the anaerobic phase
Digesting the sludge eliminates the fermentable organic material that in particular generates odors.
Degradation is achieved in an anaerobic atmosphere (i.e., without oxygen) by two fermentation pathways, acidic and methanic, each of which using distinct bacteria groups.
Acid fermentation transforms the organic material into soluble compounds, essential fatty acids, and alcohol. This also produces carbon dioxide.
Methanic fermentation products mostly methane and a lesser quantity of Carbone dioxide by further degradation of the soluble compounds.
Methane produced by the digestion process is recovered then stored in gasometers. It will be burned to produce vapor that to be used in the process and hot water that can be used for heating the space. Effluent Treatment Plant Process Odisha India
It is planned to put a thermic hydrolysis unit upstream of the digestion stage, first to liquefy the sludge and secondly to break down the longest molecular chains. The resulting mixture becomes much more easily assimilable by the digesting bacteria – “turbo-digestion”.
This thermolysis process (CAMBI®) runs at 165 °C at 8 bars pressure after the centrifuged sludge is mixed with the greases from the oil removal treatment in the biological line. Five reactors are used to do the hydrolysis.
The residue obtained, after cooling, is introduced at the digestion stages. Two structures are planned for Brussels-North, each of them equipped with a mechanical agitation system for the liquefied sludge.
On exiting the digestion stage, the sludge is directed to the oxidation unit.
Effluent Treatment Plant process Odisha India is very first growing industry right now. Produced biogas is evacuated for storage in gasometers. It can be used for the production of both vapour (hydrolysis thermal and wet oxidation) and hot water (heating of the buildings).